Si përpunohen pjesët me precizion të lartë
2023-09-22
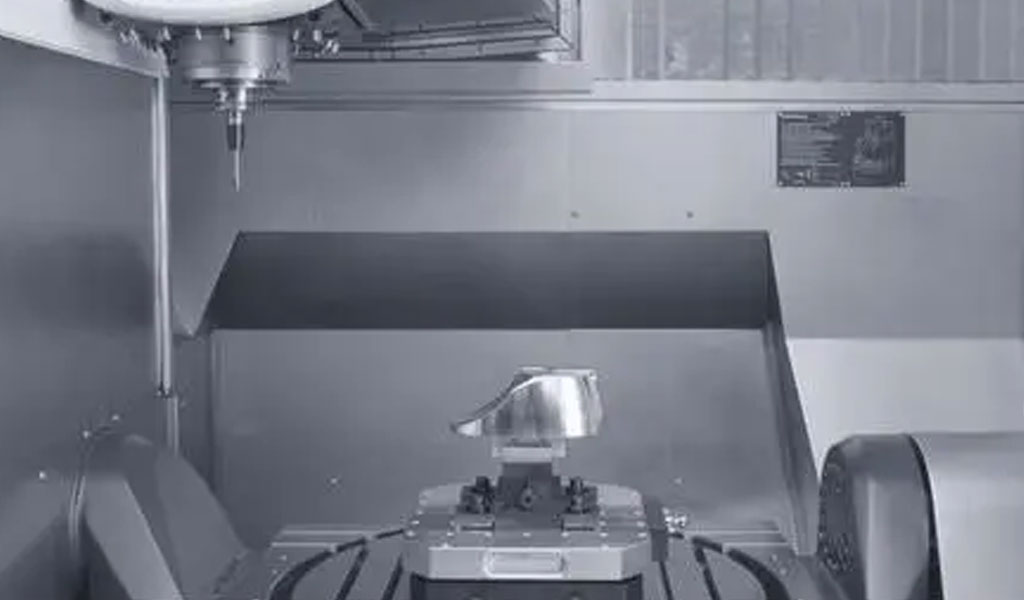
Kuptimi i përpunimit preciz
Përpunimi i saktë është një gur themeli i prodhimit modern, përgjegjës për prodhimin e komponentëve të ndërlikuar dhe të saktë të përdorur në një gamë të gjerë industrish. Për të kuptuar plotësisht domethënien e tij, le të eksplorojmë konceptet thelbësore të përpunimit me precizion, rolin e tij jetësor në sektorë të ndryshëm dhe udhëtimin historik që ka çuar në gjendjen e tij aktuale të përsosmërisë.A. Çfarë është përpunimi i saktë?
Përpunimi i saktë i referohet një grupi procesesh prodhimi që heqin materialin nga një pjesë e punës me një shkallë të lartë saktësie dhe kontrolli, duke rezultuar në komponentë të punuar imët me toleranca të ngushta. Ky proces i transformon lëndët e para, të tilla si metalet, plastika ose qeramika, në pjesë të sakta që plotësojnë specifikimet kërkuese. Karakteristikat kryesore të përpunimit të saktë përfshijnë:- Saktësi: Përpunimi i saktë siguron që produkti përfundimtar të përputhet saktësisht me dizajnin e synuar, me devijime minimale.
- Tolerancat e ngushta: Lejon prodhimin e pjesëve me toleranca jashtëzakonisht të ngushta, që do të thotë se përbërësit e përfunduar i përmbahen ngushtë matjeve të specifikuara.
- Mbarimi i sipërfaqes superiore: Përpunimi me precizion siguron përfundime të jashtëzakonshme sipërfaqësore, shpesh duke eliminuar nevojën për procese shtesë të përfundimit.
- Gjeometri komplekse: Mund të krijojë forma, konture dhe veçori të ndërlikuara, duke e bërë atë të domosdoshëm në prodhimin e komponentëve me dizajne komplekse.
- Ripërsëritshmëria: Saktësia procesi i përpunimitato janë shumë të përsëritshme, duke siguruar cilësi të qëndrueshme në pjesë të shumta.
- shkathtësi e mendjes: Mund të aplikohet në një gamë të gjerë materialesh, duke e bërë atë të përshtatshëm për industri të ndryshme.
B. Rëndësia e përpunimit preciz
Përpunimi i saktë ka një rëndësi të madhe në disa industri kritike, duke ndikuar në aspekte të ndryshme të jetës sonë të përditshme. Këtu janë disa arsye bindëse për rëndësinë e tij:- Industria e Hapësirës Ajrore: Në sektorin e hapësirës ajrore, përpunimi i saktë është i domosdoshëm për prodhimin e komponentëve që i rezistojnë kushteve ekstreme. Motorët e avionëve, ulje veshje, dhe elementët strukturorë mbështeten në pjesët e përpunuara me saktësi për siguri dhe performancë.
- Pajisjeve Mjekësore: Pajisjet mjekësore si instrumentet kirurgjikale, protezat dhe pajisjet e implantueshme kërkojnë përpunim preciz për biokompatibilitetin, saktësinë dhe sigurinë e pacientit.
- Sektori i automobilave: Pjesët e përpunuara me saktësi janë thelbësore për industrinë e automobilave për të siguruar besueshmërinë dhe efikasitetin e automjeteve. Komponentët si pjesët e motorit, sistemet e transmisionit dhe mekanizmat e frenimit mbështeten në përpunimin e saktë.
- Elektronikë dhe gjysmëpërçues: Përpunimi i saktë është thelbësor në prodhimin e komponentëve mikroelektronikë dhe pajisjeve gjysmëpërçuese, ku tolerancat e vogla janë të domosdoshme për funksionalitetin.
- Sektori i Energjisë: Industria e energjisë mbështetet në përpunimin e saktë për prodhimin e pjesëve kritike të përdorura në prodhimin e energjisë, duke përfshirë turbinat, gjeneratorët dhe komponentët e transmetimit.
- Krijimi i veglave dhe i veglave: Përpunimi i saktë është thelbësor në prodhimin e veglave dhe makinerive, të cilat, nga ana tjetër, përdoren për të krijuar produkte të tjera të panumërta.
- Consumer Electronics: Prodhimi i telefonave inteligjentë, laptopëve dhe pajisjeve të tjera elektronike të konsumit përfiton nga përpunimi i saktë për të siguruar dizajne të hijshme dhe funksionalitet optimal.
- Kërkimi dhe zhvillimi: Studiuesit dhe shkencëtarët varen nga komponentët e përpunuar me saktësi për eksperimentet, prototipet dhe pajisjet laboratorike.
C. Perspektiva historike
Udhëtimi i përpunimit preciz fillon në qytetërimet e lashta, ku artizanët e aftë përdornin mjete rudimentare për t'i dhënë formë materialeve. Megjithatë, saktësia e arritur në ato kohë ishte e kufizuar në krahasim me standardet bashkëkohore.- Përpunimi i hershëm me precizionRevolucioni industrial i shekujve 18 dhe 19 shënoi një periudhë kyçe në zhvillimin e përpunimit preciz. Shpikja e veglave të makinerive, të tilla si torno dhe frezë, revolucionarizoi prodhimin duke mundësuar saktësi dhe qëndrueshmëri më të madhe.
- Lufta e Dytë Botërore: Makineri precize luajti një rol kryesor në Luftën e Dytë Botërore, pasi ishte thelbësore për prodhimin e pajisjeve ushtarake me saktësinë dhe uniformitetin e kërkuar. Kjo epokë dëshmoi përparime në teknikat e përpunimit dhe shfaqjen e materialeve të reja.
- Përparimet e pasluftës: Periudha e pasluftës pa një rritje të inovacioneve teknologjike, duke përfshirë përdorimin e makinave kompjuterike të kontrollit numerik (CNC). Machining CNC lejohet për operacione të automatizuara dhe shumë precize, duke sjellë një epokë të re të prodhimit.
- Epoka Dixhitale: Integrimi i kompjuterëve dhe softuerëve në proceset e përpunimit e ka rritur më tej përpunimin me saktësi. Makinat moderne CNC mund të ekzekutojnë operacione komplekse me saktësi të pashoqe, duke i bërë ato të domosdoshme në peizazhin e sotëm të prodhimit.
Materialet dhe rëndësia e tyre
Materialet janë themeli i përpunimit preciz, dhe zgjedhja e materialit të duhur luan një rol kryesor në prodhimin e pjesëve me precizion të lartë. Në këtë seksion, ne do të thellojmë rëndësinë e zgjedhjes së materialeve të përshtatshme, do të kuptojmë rëndësinë e vetive të materialit dhe do të eksplorojmë faktorët e ndryshëm që ndikojnë në përpunimin.A. Përzgjedhja e Materialeve
Zgjedhja e materialeve në përpunimin me saktësi është një vendim kritik që ndikon drejtpërdrejt në performancën, qëndrueshmërinë dhe funksionalitetin e produktit përfundimtar. Prodhuesit duhet të marrin parasysh disa faktorë kur zgjedhin materiale:- Përshtatshmëria e materialit: Materiali duhet të jetë i përshtatshëm për aplikimin e synuar. Industritë dhe aplikimet e ndryshme kanë kërkesa të ndryshme, të tilla si rezistenca ndaj temperaturës, rezistenca ndaj korrozionit dhe përçueshmëria elektrike.
- Prona mekanike: Vetitë mekanike si forca në tërheqje, fortësia dhe duktiliteti janë thelbësore. Për shembull, në hapësirën ajrore, materialet me rezistencë të lartë në tërheqje preferohen për komponentët strukturorë.
- Karakteristikat termike: Disa aplikime kërkojnë materiale me përçueshmëri të shkëlqyer termike ose rezistencë ndaj temperaturave të larta. Kjo është veçanërisht e rëndësishme në industri si prodhimi i energjisë dhe elektronika.
- Rezistenca korrozioni: Në mjediset ku korrozioni është shqetësues, preferohen materialet me rezistencë të lartë ndaj korrozionit, si çelik inox ose titani.
- Konsideratat e peshës: Industritë si automobilat dhe hapësira ajrore shpesh i japin përparësi materialeve të lehta si alumini ose përbërjet e fibrave të karbonit për të reduktuar konsumin e karburantit dhe për të përmirësuar performancën.
- Kufizimet e kostos: Kostoja është një faktor i rëndësishëm në përzgjedhjen e materialit. Materialet me performancë të lartë mund të jenë të shtrenjta, kështu që prodhuesit duhet të vendosin një ekuilibër midis performancës dhe efektivitetit të kostos.
- pajtueshmërisë rregullatore: Në industri si kujdesi shëndetësor, materialet duhet të plotësojnë standarde të rrepta rregullatore për biokompatibilitetin dhe sigurinë.
- Disponueshmëri: Disponueshmëria e materialeve dhe burimet e tyre gjithashtu ndikojnë në përzgjedhjen. Disa lidhje ose përbërje të specializuara mund të kenë disponueshmëri të kufizuar.
B. Vetitë materiale
Kuptimi i vetive të materialeve është thelbësor për përpunimin me saktësi. Këtu janë disa karakteristika kryesore të materialit dhe rëndësia e tyre:- Forca elastik: Forca në tërheqje mat aftësinë e një materiali për të përballuar një forcë tërheqëse pa u thyer. Është thelbësor për komponentët strukturorë dhe pjesët që i nënshtrohen stresit mekanik.
- Fortësi: Fortësia tregon rezistencën e një materiali ndaj deformimit dhe konsumit. Materialet e forta janë të përshtatshme për veglat prerëse, ndërsa materialet më të buta mund të preferohen për aplikime të caktuara, si p.sh.
- butësi: Duktiliteti i referohet aftësisë së një materiali për të deformuar pa u thyer kur i nënshtrohet stresit në tërheqje. Materialet duktile janë më të lehta për t'u formësuar, por mund të mos jenë të përshtatshme për aplikime që kërkojnë ngurtësi.
- Përçueshmëri termike: Materialet me përçueshmëri të lartë termike shpërndajnë në mënyrë efikase nxehtësinë. Kjo veti është jetike në aplikimet ku kontrolli i temperaturës është kritik.
- Përçueshmëria elektrike: Përçueshmëria elektrike është thelbësore në elektronikë dhe komponentë elektrikë, ku materialet duhet të lehtësojnë rrjedhën e energjisë elektrike.
- Karakteristikat magnetike: Vetitë magnetike janë të rëndësishme në industri si elektromagnetika dhe elektronika, ku materialet mund të kenë nevojë të jenë ferromagnetike ose jomagnetike.
- Rezistenca kimike: Materialet duhet t'i rezistojnë korrozionit kimik në mjedise ku janë të ekspozuar ndaj acideve, bazave ose substancave të tjera gërryese.
C. Faktorët e përpunimit
Përpunueshmëria i referohet lehtësisë me të cilën një material mund të përpunohet, pritet ose formohet. Ai ndikohet nga faktorë të ndryshëm, duke përfshirë:- Fortësia e materialit: Materialet më të buta janë përgjithësisht më të lehta për t'u përpunuar, ndërsa materialet më të forta mund të kërkojnë mjete dhe teknika të specializuara.
- Formimi i Çipit: Formimi dhe evakuimi i patate të skuqura gjatë përpunimit ndikon në efikasitetin e procesit dhe përfundimin e sipërfaqes.
- Veshja e veglave: Materialet e ndryshme mund të shkaktojnë shkallë të ndryshme të konsumimit të veglave, duke ndikuar në shpejtësinë dhe koston e përpunimit.
- Ftohës dhe lubrifikimi: Ftohësi dhe lubrifikimi i duhur janë thelbësorë për të reduktuar fërkimin, nxehtësinë dhe konsumimin e veglave gjatë përpunimit.
- Prerja e shpejtësisë: Shpejtësia me të cilën vegla prerëse lëviz nëpër material ndikon si në produktivitetin ashtu edhe në cilësinë e sipërfaqes së përpunuar.
- Materiali i veglave: Zgjedhja e materialit të veglave prerëse, si karabit ose çeliku me shpejtësi të lartë, varet nga materiali që përpunohet.
- Parametrat e prerjes: Rregullimi i parametrave të prerjes si shpejtësia e ushqimit dhe thellësia e prerjes mund të optimizojë procesin e përpunimit për materiale specifike.
Vegla makinerish për përpunim preciz
Veglat e makinerive janë zemra e përpunimit me precizion, duke mundësuar transformimin e lëndëve të para në pjesë me precizion të lartë. Në këtë seksion, ne do të eksplorojmë katër lloje kryesore të veglave të makinerive të përdorura në përpunimin me saktësi: Qendrat e përpunimit CNC, Makinat rrotulluese, Makinat bluarëse dhe EDM (Përpunimi me shkarkimin elektrik). Secila prej këtyre makinave luan një rol unik në prodhimin e komponentëve të saktë.A. Qendrat e përpunimit CNC
Qendrat e përpunimit CNC (Computer Numerical Control) janë të gjithanshme dhe përdoren gjerësisht në përpunimin me saktësi. Ato janë sisteme të automatizuara që kontrollojnë lëvizjen e veglave prerëse dhe pjesëve të punës me saktësi të jashtëzakonshme. Këtu është një përmbledhje e qendrave të përpunimit CNC dhe rëndësia e tyre:- shkathtësi e mendjes: Qendrat e përpunimit CNC mund të kryejnë operacione të ndryshme përpunimi, duke përfshirë bluarjen, shpimin dhe prerjen. Kjo shkathtësi lejon prodhimin e pjesëve komplekse me karakteristika të shumta.
- Saktësi e madhe: Kontrolli i kompjuterizuar i makinerive CNC siguron pozicionim të saktë të veglave dhe rezultate të qëndrueshme, duke i bërë ato ideale për pjesët me toleranca të ngushta.
- Automatizim: Qendrat e përpunimit CNC mund të funksionojnë vazhdimisht, me ndërhyrje minimale njerëzore. Ky automatizim rrit efikasitetin dhe zvogëlon rrezikun e gabimeve.
- Gjeometri komplekse: Ata shkëlqejnë në përpunimin e formave dhe kontureve të ndërlikuara, duke i bërë ato të përshtatshme për industri si hapësira ajrore, ku komponentët kompleksë janë të zakonshëm.
- Rezultate të përsëritshme: Makinat CNC ofrojnë përsëritshmëri të shkëlqyer, duke siguruar që çdo pjesë e prodhuar të përputhet me specifikimet e sakta të dizajnit.
- Kohët e reduktuara të konfigurimit: Qendrat e përpunimit CNC mund të programohen për të kaluar shpejt ndërmjet detyrave të ndryshme, duke minimizuar kohën e konfigurimit dhe duke rritur efikasitetin e prodhimit.
B. Makinat rrotulluese
Makinat rrotulluese përdoren për të krijuar pjesë cilindrike duke rrotulluar një pjesë të punës ndërsa një mjet prerës heq materialin nga sipërfaqja e tij e jashtme. Ato janë thelbësore për prodhimin boshts, kunjat dhe komponentët e tjerë me simetri rrotulluese. Pikat kryesore në lidhje me makinat rrotulluese përfshijnë:- Pjesë cilindrike: Makinat tornuese specializohen në prodhimin e komponentëve cilindrikë ose tuba, duke përfshirë ato me fije ose brazda të ndërlikuara.
- Shpejtësi të larta: Ata funksionojnë me shpejtësi të lartë, duke i bërë të përshtatshme për pjesët që kërkojnë një përfundim të qetë dhe të saktë.
- Operacioni me një aks: Shumica e makinave tornuese janë me një bosht, duke u fokusuar në formësimin e sipërfaqes së jashtme të pjesës së punës.
- Efikas për prodhim masiv: Kthimi është shumë efikas për prodhimin në masë të pjesëve me mbetje materiale minimale.
- Makina torno: Makinat e tornove manuale dhe të kontrolluara me CNC janë makina torno që përdoren zakonisht, duke ofruar një sërë aftësish.
C. Makinat bluarëse
Makinat bluarëse janë të dizajnuara për përfundimin e saktë të sipërfaqes dhe formësimin e materialeve të forta ose gërryese. Ato janë thelbësore për arritjen e tolerancave jashtëzakonisht të ngushta dhe përfundimeve superiore të sipërfaqes. Ja pse makinat bluarëse janë të rëndësishme:- Precision në nivel mikron: Makinat bluarëse mund të arrijnë saktësi në nivel mikron, duke i bërë ato thelbësore për aplikimet që kërkojnë saktësinë më të lartë.
- Largimi i materialit: Ata heqin materialin me gërryerje, duke lejuar korrigjimin e papërsosmërive të sipërfaqes dhe duke arritur një butësi të jashtëzakonshme.
- Bluarje veglash dhe prerëse: Përveç bluarjes sipërfaqësore, ekzistojnë makina bluarëse të specializuara për mprehjen e veglave prerëse dhe prodhimin e profileve të sakta.
- Shumëllojshmëria e metodave të bluarjes: Llojet e ndryshme të makinerive bluarëse, duke përfshirë bluarjet sipërfaqësore, bluajtësit cilindrikë dhe mullinjtë pa qendër, plotësojnë nevoja të ndryshme përpunimi.
- Materialet e ngurtësuara: Bluarja është veçanërisht e përshtatshme për materialet e ngurtësuara si çeliku i veglave dhe qeramika, ku metodat tradicionale të përpunimit mund të jenë joefektive.
D. EDM (përpunimi i shkarkimit elektrik)
EDM, ose Përpunimi me Shkarkim Elektrik, është një proces përpunimi jo tradicional që përdor shkarkimet elektrike për t'i dhënë formë materialeve. Është ideale për krijimin e pjesëve të ndërlikuara dhe delikate ku mjetet tradicionale prerëse mund të shkaktojnë dëme. Aspektet kryesore të EDM përfshijnë:- Asnjë kontakt fizik: EDM nuk përfshin kontakt të drejtpërdrejtë fizik midis veglës dhe pjesës së punës, duke minimizuar rrezikun e konsumimit të veglës dhe dëmtimit të materialeve të brishta.
- Saktësi e madhe: Mund të arrijë saktësi të lartë dhe cilësi të përfundimit të sipërfaqes, edhe me materiale jashtëzakonisht të forta.
- Teli EDM dhe Sinker EDM: Ekzistojnë dy lloje kryesore të makinave EDM: prerja e telit EDM, e cila përdor një elektrodë teli dhe EDM sinker, e cila përdor një elektrodë në formë.
- Forma komplekse: EDM mund të prodhojë forma komplekse, të tilla si kallëpe dhe kallëpe, me detaje të ndërlikuara dhe karakteristika të shkëlqyera.
- Zona e prekur nga nxehtësia: Meqenëse EDM nuk gjeneron nxehtësi në pjesën e punës, është i përshtatshëm për materiale të ndjeshme ndaj nxehtësisë si lidhjet e hapësirës ajrore.
- Procesi i ngadalshëm: EDM është relativisht i ngadaltë në krahasim me metodat e tjera të përpunimit, duke e bërë atë më të përshtatshme për punë me sasi të ulët dhe me saktësi të lartë.
Mjetet e prerjes dhe përpunimit
Veglat prerëse janë në krye të përpunimit me precizion, duke shërbyer si instrumente që formojnë dhe transformojnë lëndët e para në pjesë me precizion të lartë. Në këtë seksion, ne do të shqyrtojmë llojet e ndryshme të veglave prerëse, rëndësinë e veshjeve të veglave dhe faktorët që ndikojnë në jetëgjatësinë dhe konsumimin e veglave.A. Llojet e veglave prerëse
Përpunimi i saktë mbështetet në një gamë të larmishme veglash prerëse, secila e projektuar për detyra dhe materiale specifike. Zgjedhja e mjetit prerës ndikon shumë në efikasitetin dhe saktësinë e procesit të përpunimit. Këtu janë disa lloje të zakonshme të mjeteve prerëse:- Fund Mills: Mullinjtë fundorë janë mjete të gjithanshme që përdoren për operacionet e bluarjes. Ata kanë skaje të shumta prerëse dhe mund të heqin materialin nga pjesa e punës në mënyra të ndryshme, duke përfshirë ballafaqimin, konturimin dhe vrimën.
- Drills: Stërvitjet janë të dizajnuara për krijimin e vrimave në pjesët e punës. Ato vijnë në forma të ndryshme, duke përfshirë stërvitje me kthesë, stërvitje qendrore dhe stërvitje të indeksueshme.
- Futjet rrotulluese: Këto përdoren në makinat tornuese për të formuar pjesët cilindrike. Insertet rrotulluese janë të disponueshme në forma dhe materiale të ndryshme për t'iu përshtatur aplikacioneve të ndryshme.
- Freza: Frezuesit vijnë në forma të ndryshme, të tilla si mullinjtë e fytyrës, mullinjtë me top dhe prerëset me prerje, dhe përdoren në makinat bluarëse për të krijuar veçori të ndryshme në pjesën e punës.
- Reamers: Mbajtësit përdoren për përfundimin dhe përmasimin e vrimave të shpuara më parë në dimensione të sakta. Ato sigurojnë sipërfaqe të lëmuara dhe të sakta të vrimave.
- Prek dhe vdes: Këto mjete prerëse përdoren për operacionet e filetimit. Trokitjet krijojnë fije të brendshme, ndërsa makineritë krijojnë fije të jashtme.
- Rrota bluarje: Rrotat bluarëse janë vegla gërryese që përdoren për bluarje me saktësi të sipërfaqes. Ato janë të disponueshme në materiale të ndryshme gërryese dhe madhësi zhavorri.
- Broaches: Broshat janë vegla të specializuara që përdoren për prerjen e formave dhe profileve të brendshme dhe të jashtme, të tilla si çelësa dhe spina.
- Kundërbore dhe kundërlava: Këto mjete përdoren për të krijuar gropa ose anime rreth vrimave për shuls.
- Bare të mërzitshme: Shufrat e mërzitshme përdoren në operacionet e mërzitshme për të zgjeruar vrimat ekzistuese me saktësi.
B. Veshjet e veglave
Veshjet e veglave janë shtresa të holla materiali të aplikuara në veglat prerëse për të rritur performancën dhe qëndrueshmërinë e tyre. Këto veshje ofrojnë disa përparësi:- Fërkimi i reduktuar: Veshjet si nitridi i titanit (TiN) dhe karbonitridi i titanit (TiCN) zvogëlojnë fërkimin midis veglës dhe pjesës së punës, duke çuar në prerje më të butë dhe jetëgjatësi më të gjatë të veglave.
- Fortësi e rritur: Veshjet rrisin fortësinë e sipërfaqes së veglës, duke e bërë atë më rezistente ndaj konsumit dhe duke zgjatur jetën e veglës.
- Rezistencë e përmirësuar ndaj nxehtësisë: Veshjet mund t'i rezistojnë temperaturave të larta të krijuara gjatë përpunimit, duke reduktuar konsumin e veglave të lidhura me nxehtësinë dhe duke rritur shpejtësinë e prerjes.
- Vetitë kundër ndërtimit: Disa veshje kanë veti kundër ngjitjes, duke parandaluar grumbullimin e materialit në skajet prerëse të veglës.
- Lubriciteti i rritur: Veglat e veshura kanë përmirësuar lubricitetin, duke reduktuar nevojën për ftohës të tepërt dhe duke rritur evakuimin e çipave.
C. Jeta dhe veshja e veglave
Kuptimi i jetëgjatësisë dhe konsumit të veglave është thelbësor për optimizimin e proceseve të përpunimit dhe minimizimin e kostove të prodhimit. Jetëgjatësia e veglës i referohet kohëzgjatjes që një mjet prerës mbetet efektiv përpara se të kërkojë zëvendësim ose rindërtim. Disa faktorë ndikojnë në jetëgjatësinë dhe konsumimin e veglave:- Prerja e shpejtësisë: Shpejtësitë më të larta të prerjes mund të çojnë në konsum të shtuar të veglave për shkak të temperaturave më të larta të krijuara gjatë përpunimit. Zgjedhja e duhur e shpejtësive të prerjes është thelbësore për të balancuar jetëgjatësinë dhe produktivitetin e mjetit.
- Norma e Feed: Shpejtësia me të cilën mjeti prerës përparon në pjesën e punës ndikon në konsumimin e veglave. Shkalla e lartë e furnizimit mund të përshpejtojë konsumimin, ndërsa nivelet më të ulëta të furnizimit mund të zgjasin jetën e veglës.
- Thellësia e prerjes: Thellësia e prerjes ndikon në sasinë e materialit të hequr për kalim. Prerjet më të thella mund të rrisin konsumin e veglave, kështu që optimizimi i thellësisë është kritik.
- Fortësia e materialit: Prerja e materialeve të forta mund të përshpejtojë konsumimin e veglave. Mjetet dhe veshjet e specializuara përdoren për përpunimin efektiv të materialeve të forta.
- Ftohës dhe lubrifikimi: Ftohësi dhe lubrifikimi i duhur ndihmojnë në shpërndarjen e nxehtësisë dhe zvogëlimin e fërkimit, duke zgjatur jetën e mjetit.
- Materiali i veglave: Materiali nga i cili është bërë mjeti prerës ndikon në rezistencën e tij ndaj konsumit. Materialet si karbidi dhe qeramika ofrojnë rezistencë të shkëlqyer ndaj konsumit.
- Gjeometria e veglave: Gjeometria e veglës prerëse, duke përfshirë këndin e grabitjes, këndin e lehtësimit dhe modelin e thyerësit të çipave, luan një rol të rëndësishëm në modelet e veshjes.
- Materiali i pjesës së punës: Lloji i materialit që përpunohet ndikon në konsumimin e veglave. Materialet gërryese mund të çojnë në konsumim më të shpejtë të veglave.
Proceset e përpunimit preciz
Proceset e përpunimit me precizion janë metodat me të cilat lëndët e para shndërrohen në pjesë me precizion të lartë me toleranca të ngushta dhe përfundime të jashtëzakonshme sipërfaqësore. Në këtë seksion, ne do të eksplorojmë pesë procese kyçe të përpunimit me saktësi: Kthyerja, Frezimi, Shpimi, Bluarja dhe Përpunimi me Shkarkim Elektrik (EDM). Secili prej këtyre proceseve i shërben një qëllimi unik dhe përdoret në bazë të kërkesave specifike të pjesës së punës.A. Duke u kthyer
Kthimi është një proces përpunimi që përdoret kryesisht për formimin e pjesëve cilindrike. Ai përfshin rrotullimin e një pjese të punës ndërsa një mjet prerës me një pikë heq materialin nga sipërfaqja e jashtme. Këtu janë aspektet kryesore të kthesës:- Pjesë cilindrike: Kthimi është ideal për prodhimin e komponentëve cilindrikë si boshtet, kunjat dhe mëngët.
- Simetria rrotulluese: Është i përshtatshëm për pjesët që kërkojnë simetri rrotulluese, pasi pjesa e punës rrotullohet në një torno ndërsa mjeti prerës i jep formë.
- Operacione të ndryshme: Kthimi mund të kryejë operacione të ndryshme, duke përfshirë ballafaqimin, kthimin (zvogëlimin e diametrit), kthimin me kon dhe filetimin.
- Prerje me një pikë: Një mjet i vetëm prerës heq materialin në një lëvizje të vazhdueshme, duke rezultuar në heqjen efikase të materialit.
- Makina torno: Si makineritë manuale ashtu edhe ato të kontrolluara me CNC përdoren zakonisht për torno.
B. Mulliri
Mulliri është një proces i gjithanshëm i përpunimit me saktësi që përdor mjete prerëse me shumë pika për të hequr materialin nga një pjesë e punës. Është i përshtatshëm për krijimin e një game të gjerë formash dhe veçorish. Aspektet kryesore të bluarjes përfshijnë:- shkathtësi e mendjes: Frezimi mund të prodhojë sipërfaqe të sheshta, vrima, xhepa dhe konture komplekse. Përdoret për përpunimin 2D dhe 3D.
- Prerje me shumë pika: Tehe të shumta prerëse në mjet ndërveprojnë me pjesën e punës njëkohësisht, duke lejuar heqjen efikase të materialit.
- Llojet e bluarjes: Frezimi mund të kryhet duke përdorur lloje të ndryshme prerësesh, duke përfshirë mullirin fundor, mullirin e fytyrës dhe mullirin me top.
- Qendrat e përpunimit CNC: Makinat e bluarjes të kontrolluara me CNC ofrojnë kontroll të saktë mbi lëvizjen e veglave dhe përdoren gjerësisht në përpunimin modern.
- Shpejtësi të larta: Frezimi mund të kryhet me shpejtësi të lartë, duke mundësuar prodhim efikas.
C. Shpimi
Shpimi është një proces përpunimi i saktë i përdorur për të krijuar vrima në pjesët e punës. Është një operacion themelor në industri të ndryshme. Aspektet kryesore të shpimit përfshijnë:- Krijimi i vrimës: Makinat e shpimit përdorin mjete të specializuara të quajtura shpuese për të hequr materialin dhe për të krijuar vrima me diametra të caktuar.
- Llojet e stërvitjeve: Ekzistojnë lloje të ndryshme stërvitjesh, duke përfshirë stërvitjet me rrotullim, stërvitjet qendrore dhe stërvitjet e indeksueshme, secila e krijuar për aplikime specifike.
- Saktësi: Pozicionimi dhe shtrirja e saktë janë thelbësore në shpime për të siguruar që vrimat të krijohen me saktësi.
- Shpejtësia dhe shkalla e furnizimit: Parametrat e shpimit si shpejtësia e rrotullimit dhe shpejtësia e futjes janë kritike për arritjen e dimensioneve të dëshiruara të vrimave.
- Ftohës dhe lubrifikimi: Ftohësi dhe lubrifikimi i duhur përdoren për të shpërndarë nxehtësinë dhe për të zvogëluar fërkimin gjatë shpimit.
D. Bluarje
Bluarja është një proces përpunimi i saktë që përdor rrota gërryese për të hequr materialin dhe për të arritur toleranca jashtëzakonisht të ngushta dhe përfundime të sipërfaqes. Aspektet kryesore të bluarjes përfshijnë:- Precizion i jashtëzakonshëm: Bluarja mund të arrijë saktësi në nivel mikron, duke e bërë atë ideal për aplikime që kërkojnë saktësinë më të lartë.
- Finish Sipërfaqja: Prodhon përfundime superiore sipërfaqësore, shpesh duke eliminuar nevojën për procese shtesë të përfundimit.
- Materiale: Bluarja është e përshtatshme për materiale të forta dhe gërryese, duke përfshirë çelikun e ngurtësuar, qeramikën dhe karbidet.
- Shumëllojshmëria e metodave të bluarjes: Llojet e ndryshme të makinerive bluarëse, të tilla si bluarjet sipërfaqësore, bluarjet cilindrike dhe mullinjtë pa qendër, plotësojnë nevoja të ndryshme përpunimi.
- Ftohës: Ftohësi i duhur është thelbësor në bluarje për të parandaluar mbinxehjen dhe për të ruajtur integritetin e rrotave.
E. Përpunimi me shkarkimin elektrik (EDM)
EDM, ose Përpunimi me Shkarkim Elektrik, është një proces jo-tradicional i përpunimit me saktësi që përdor shkarkimet elektrike për të hequr materialin. Ai është veçanërisht i përshtatshëm për përpunimin e formave komplekse dhe të ndërlikuara, si dhe për materiale të forta dhe rezistente ndaj nxehtësisë. Aspektet kryesore të EDM përfshijnë:- Përpunimi pa kontakt: EDM nuk përfshin kontakt të drejtpërdrejtë midis veglës dhe pjesës së punës, duke zvogëluar rrezikun e konsumimit dhe dëmtimit të veglës.
- Saktësi e madhe: EDM mund të arrijë saktësi të lartë, duke e bërë atë të përshtatshëm për aplikime ku tolerancat e ngushta janë thelbësore.
- Forma komplekse: Shkëlqen në përpunimin e formave komplekse, makinerive, kallëpeve dhe komponentëve me detaje të imta.
- Teli EDM dhe Sinker EDM: Ekzistojnë dy lloje kryesore të makinave EDM: EDM me tela, e cila përdor një elektrodë teli dhe EDM sinker, e cila përdor një elektrodë në formë.
- Procesi i ngadalshëm: EDM është relativisht i ngadaltë në krahasim me metodat e tjera të përpunimit, duke e bërë atë më të përshtatshme për punë me sasi të ulët dhe me saktësi të lartë.
Tolerancat dhe Kontrolli i Cilësisë
Përpunimi i saktë kërkon vëmendje të përpiktë ndaj detajeve dhe një angazhim rigoroz për kontrollin e cilësisë për të siguruar që pjesët plotësojnë standardet e specifikuara. Në këtë seksion, ne do të eksplorojmë tre aspekte kritike të kontrollit të cilësisë në përpunimin me saktësi: Dimensionimi dhe Toleranca Gjeometrike (GD&T), Kontrolli i Procesit Statistikor (SPC) dhe Sigurimi i Cilësisë.A. Dimensionimi dhe toleranca gjeometrike (GD&T)
Dimensionimi dhe Toleranca Gjeometrike, shpesh e shkurtuar si GD&T, është një sistem që përdoret për të përcaktuar dhe komunikuar variacionet e lejuara në madhësi, formë, orientim dhe vendndodhje të veçorive në një pjesë. GD&T është jetik në përpunimin me saktësi për arsyet e mëposhtme:- Komunikimi i saktë: GD&T ofron një gjuhë të standardizuar për inxhinierët, projektuesit dhe makinistët për të komunikuar me saktësi qëllimin e projektimit dhe kërkesat dimensionale.
- Sqarim i Tolerancës: Ndihmon në përcaktimin e variacionit të pranueshëm në dimensionet kritike, duke siguruar që të gjithë palët e interesuara të kuptojnë devijimet e lejueshme.
- Cilësi e përmirësuar: GD&T promovon cilësi të përmirësuar duke reduktuar paqartësitë në specifikimet e projektimit, duke minimizuar rrezikun e gabimeve gjatë përpunimit.
- Efikasiteti i kostos: Specifikimet e qarta të GD&T mund të çojnë në uljen e kostove të prodhimit, pasi pjesët kanë më pak gjasa të hiqen ose të kërkojnë ripunim për shkak të keqkuptimit ose keqinterpretimit.
- Gjeometri komplekse: Është veçanërisht i dobishëm për pjesët me gjeometri komplekse, duke siguruar që të gjitha veçoritë të jenë prodhuar sipas specifikimeve të dëshiruara.
B. Kontrolli i Procesit Statistikor (SPC)
Kontrolli i Procesit Statistikor (SPC) është një metodologji e kontrollit të cilësisë që përdor teknika statistikore për të monitoruar dhe kontrolluar procesin e përpunimit. SPC është thelbësor në përpunimin me saktësi për arsyet e mëposhtme:- Monitorimi i procesit: SPC ndihmon në monitorimin e proceseve të përpunimit në kohë reale, duke identifikuar variacionet ose devijimet nga parametrat e dëshiruar.
- Zbulimi i hershëm i çështjeve: Duke monitoruar vazhdimisht procesin, SPC lejon zbulimin e hershëm të çështjeve që mund të çojnë në pjesë jashtë specifikave, duke reduktuar mbeturinat dhe ripërpunimin.
- Vendimmarrja e Drejtuar nga të Dhënat: SPC mbështetet në të dhëna dhe analiza statistikore për të marrë vendime të informuara në lidhje me rregullimet e procesit, duke siguruar që procesi i përpunimit të mbetet brenda kufijve të pranueshëm.
- Konsistenca e përmirësuar: SPC promovon konsistencën e procesit dhe zvogëlon gjasat e prodhimit të pjesëve që nuk përputhen.
- Reduktuar skrap dhe ripunim: Duke identifikuar dhe adresuar shpejt variacionet e procesit, SPC minimizon prodhimin e pjesëve me defekt, duke reduktuar kostot e skrapit dhe ripërpunimit.
C. Sigurimi i cilësisë në përpunimin preciz
Sigurimi i cilësisë në përpunimin e saktë përfshin një qasje gjithëpërfshirëse për të siguruar që pjesët e prodhuara plotësojnë ose tejkalojnë standardet e specifikuara të cilësisë. Ai përfshin elementë të ndryshëm, duke përfshirë:- Dokumentacioni i procesit: Dokumentacioni i detajuar i proceseve të përpunimit, duke përfshirë procedurat standarde të funksionimit (SOP) dhe udhëzimet e punës, siguron që çdo hap të kryhet në mënyrë konsistente.
- Inspektimi dhe Matja: Inspektimi dhe matja rigoroze duke përdorur instrumente precize dhe teknika metrologjike verifikon që pjesët përputhen me tolerancat dhe standardet e cilësisë së specifikuar.
- Kalibrim: Kalibrimi i rregullt i pajisjeve të përpunimit dhe instrumenteve matëse është thelbësor për të ruajtur saktësinë dhe gjurmueshmërinë.
- Verifikimi i materialit: Verifikimi i vetive, përbërjes dhe cilësisë së materialit është thelbësor për të siguruar që materiali i përdorur plotëson kërkesat e projektimit.
- Trajnimi i punonjësve: Programet e trajnimit dhe zhvillimit të aftësive për makinistët dhe personelin e kontrollit të cilësisë sigurojnë që ata të jenë të aftë në rolet dhe përgjegjësitë e tyre.
- Analiza e shkakut rrënjësor: Kur identifikohen pjesë që nuk përputhen, bëhet analiza e shkakut rrënjësor për të përcaktuar burimin e problemit dhe për të zbatuar veprime korrigjuese.
- Përmirësimi i vazhdueshëm: Një kulturë e përmirësimit të vazhdueshëm nxit inovacionin dhe nxit përmirësime të vazhdueshme në proceset e përpunimit dhe procedurat e kontrollit të cilësisë.
- Feedback konsumatorëve: Mbledhja dhe analizimi i komenteve të klientit ndihmon në identifikimin e fushave për përmirësim dhe përafron proceset e përpunimit me pritshmëritë e klientit.
Përfundim
A. Arti dhe shkenca e përpunimit preciz
Përpunimi i saktë qëndron në kryqëzimin e artit dhe shkencës, ku kreativiteti, aftësia dhe inovacioni konvergojnë për të prodhuar pjesë me saktësi të lartë që drejtojnë industritë dhe formësojnë botën moderne. Është njëkohësisht një formë arti, që kërkon mjeshtërinë dhe ekspertizën e makinistëve që transformojnë lëndët e para në vepra të përsosmërisë inxhinierike, dhe një shkencë që mbështetet në teknologjinë e fundit, shkencën e materialeve dhe proceset e avancuara për të arritur saktësi të pashoqe. Udhëtimi i përpunimit të saktë na çon përmes të kuptuarit të materialeve dhe vetive të tyre, zotërimit të veglave dhe makinerive prerëse dhe kontrollit të përpiktë të proceseve dhe tolerancave. Ai përfshin gjuhën e dimensionimit dhe tolerancës gjeometrike, vigjilencën e kontrollit të procesit statistikor dhe përkushtimin për sigurimin e cilësisë. Përpunimi me precizion luan një rol kryesor në industri të ndryshme, nga hapësira ajrore dhe automobilistike tek pajisjet mjekësore dhe elektronika, duke formuar gjithçka, nga motorët e avionëve deri te nyjet artificiale dhe mikroçipet. Ai mundëson krijimin e komponentëve që funksionojnë me saktësi dhe besueshmëri të pakrahasueshme, shpesh duke shtyrë kufijtë e asaj që është e mundur.B. Mendimet përfundimtare
Ndërsa përfundojmë këtë eksplorim të përpunimit preciz, është e qartë se kjo fushë nuk ka të bëjë vetëm me krijimin e pjesëve; bëhet fjalë për krijimin e mundësive. Kërkimi për saktësi nxit inovacionin, duke shtyrë kufijtë e asaj që mund të arrihet. Pavarësisht nëse është mjeshtëria delikate e nevojshme për të krijuar ingranazhet e ndërlikuara të një ore ose teknologjia e avancuar e nevojshme për prodhimin e komponentëve komplekse të hapësirës ajrore, përpunimi i saktë është në zemër të të gjithave. E ardhmja e përpunimit preciz është e mbushur me premtime. Përparimet në shkencën e materialeve, automatizimin dhe teknologjitë dixhitale vazhdojnë të riformësojnë peizazhin. Miniaturizimi, printimi 3D dhe praktikat e prodhimit të qëndrueshëm po bëhen gjithnjë e më të spikatura, duke hapur horizonte të reja për industrinë. Në një botë ku saktësia ka më shumë rëndësi se kurrë, përpunimi i saktë mbetet një shtyllë e domosdoshme e inxhinierisë moderne. Është një dëshmi e zgjuarsisë njerëzore dhe e ndjekjes sonë të paepur për përsosmëri në çdo aspekt të prodhimit. Ndërsa kërkesa për saktësi më të lartë dhe komponentë më të ndërlikuar rritet, përpunimi me precizion do të vazhdojë të evoluojë, duke përmbushur sfidat e së nesërmes me të njëjtin përkushtim dhe saktësi që e kanë përcaktuar atë për shekuj.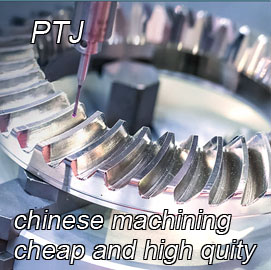
Shërbimet tona
- 5 Përpunimi i boshtit
- Mulliri Cnc
- Duke u kthyer
- Industritë e përpunimit
- Procesi i përpunimit
- Trajtim sipërfaqësor
- Machining Metal
- Përpunimi i plastikës
- Mould Metalurgji pluhur
- Die Kallëp
- Galeria e Pjesëve
Raste Studimore
- Pjesë metalike automatike
- Pjesë makinerie
- Heatsink LED
- Pjesë Ndërtimi
- Pjesë celulare
- Pjesë mjekësore
- Pjesë elektronike
- Përpunimi i përshtatur
- Pjesë Biciklete
Lista e materialeve
- Përpunimi i aluminit
- Përpunimi i titanit
- Përpunimi i çelikut inox
- Përpunimi i bakrit
- Përpunimi prej bronzi
- Përpunim Super Aliazh
- Shikim Makineri
- Përpunim UHMW
- Makineri Unilate
- PA6 Makineri
- PPS përpunim
- Përpunimi i Teflonit
- Machon Inconel
- Vegla për përpunimin e çelikut
- Më shumë material
Galeria e Pjesëve